Automatic controllers have been in use in some form or another for many years. Things are a little different today, but the basic concept has remained the same: Provide feedback among moving parts.
Modern industrial controller systems
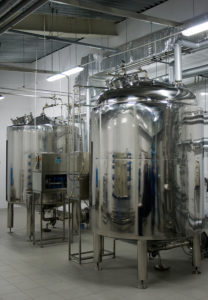
Today’s controllers fall into several forms. Programmable logic controllers (PLCs) began as simple relay systems but have evolved into robust, easily programmable minicomputers that can assimilate data and return results even in harsh environments. They do not, however, handle complex data very well.
Programmable automation controllers (PACs) have programming advantages over PLCs and can easily interface with other systems and with direct users. A distributed control system (DCS) is spread throughout the machine, controlling various parts and functions as opposed to PLCs or PACs, which control only one function. PC-based control systems allow for input from various field locations to calculate the appropriate mechanical responses. Embedded board level controllers take up less space than other controllers but pack more power into that space.
Controller change through the years
As with any system, programmers have changed controllers over the years to adapt to new technologies: Manual systems automated; automated systems integrated and communicated with other systems; and integrated systems took advantage of internet connectivity. With each change, developers created controller systems with greater capacities to process data and different input types, depending on end users’ needs.
However, today’s wireless technology can come with its own risks, including data breaches and holding data for ransom as well as downtime due to technological failures.
Key controller features
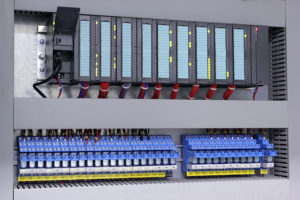
The National Institutes of Standards and Technology developed security guidelines for federal information systems that are equally applicable to manufacturing company controller systems. These guidelines provide common-sense recommendations for handling network and security issues such as limiting data flow into controllers, protecting individual components from corruption, separating credentials for individual users, and creating a continuity-of-operations plan in case of a security breach.
Scalability plays an important role in control systems. Programmers may begin to automate one portion before automating the remainder when affordable. System integration and internet connectivity create the ability to upscale initial systems as required.
Modifiability, or the ability to easily make changes to an original plan, provides the flexibility to customize controller plans.
Controller system case study
According to an Applied Automation article, Clarksville, Arkansas, city leaders knew they needed to upgrade their utility system. After carefully evaluating their wireless capacity, they chose a secure internal network to accommodate supervisory control and data acquisition (SCADA). Combining water, wastewater, and power systems into one cybersecure platform allows both remote and user data input. The controller system will be able to grow as the city grows, continuing to meet residents’ needs.
While this system worked well for Clarksville, it’s not necessarily the perfect solution for every situation. If you perform extensive field work, you may want to consider a PC-based system. If your remote locations experience harsh weather, you might want to go with either PLCs or PACs. Consult a professional who can help you determine your needs and the system that’s right for you.
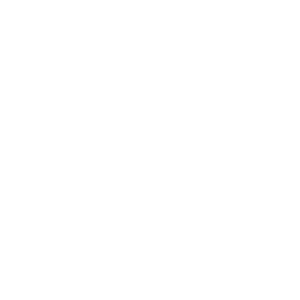