“I cannot imagine any condition which could cause a ship to founder. I cannot conceive of any vital disaster happening to this vessel. Modern shipbuilding has gone beyond that.” — EJ Smith, Captain, RMS Titanic
While most of us will never experience an accident of Titanic proportions, workplace safety should be the top priority in our plants. Safety increases morale and productivity. A safe worker is a happy worker. And, if implemented properly and reinforced daily, safety procedures such as proper equipment maintenance and repair improve your bottom line. According to the U.S. Department of Labor, workplace incidents cost employers nearly $1 billion annually in workers’ compensation costs.
Early workplaces
Of course, this wasn’t always the prevailing wisdom in factory work. Before the U.S. government enacted child labor laws, 1.75 million children between the ages of 10 and 15 were employed. Current labor law prohibits children under age 16 from working full time.
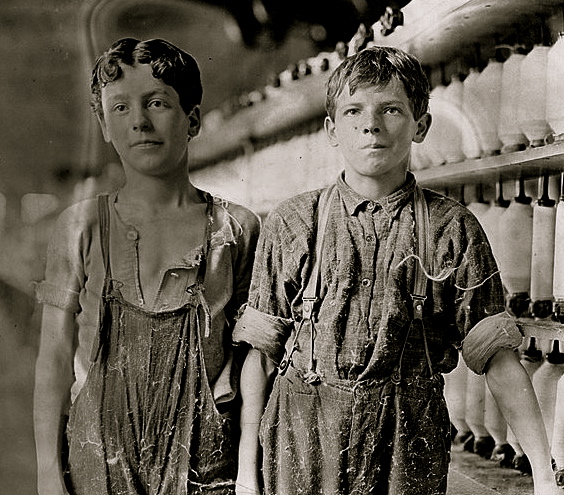
At the turn of the last century, the average work week lasted approximately 53 hours. Now, the standard work week is 40 hours with many employers providing paid vacation, sick leave, and medical benefits. For those unfortunate individuals who were injured on the job prior to modern labor laws, their only recourse was to find another means of support or to rely on the kindness of others. Today, workers’ compensation, short- and long-term disability benefits, and other social safety nets ensure injured workers’ well-being.
With no financial incentive to create a safe workplace, most employers once chose to take their chances regarding workplace injuries. It was less expensive to pay the relatively few successful death or injury claims required of them than it was to implement safety procedures. With the dawn of the Industrial Revolution, workplace injuries became more common as increasingly complex and often dangerous machinery entered manufacturing floors. A combination of labor unions, journalists, and reformers pressed for — and succeeded in creating — industrial safety regulations making it more expensive for companies to disregard workers’ welfare.
OSHA
The single largest contribution to workers’ well-being was the Occupational Safety and Health (OSHA) Act enactment in 1970. Prior to OSHA, state laws regulated workplace safety. But these laws often contained loopholes and rarely kept pace with increasing employment hazards. The General Duty Clause placed the onus on employers for the safety of anyone within manufacturing facility buildings or grounds.
Because of OSHA, workers can report unsafe practices to their supervisors for remediation without fear of reprisal. Employers now train workers to operate machinery safely and provide proper protective gear. They also practice other simple safety measures such as cleaning spills and ensuring that work spaces are hazard-free to prevent slip, trip, or fall accidents. A few additional safety tips include using proper posture when lifting and remembering to take breaks. A tired employee is a careless employee. And most manufacturers now recognize that properly maintained equipment is less likely to malfunction and injure employees.