Contrary to popular belief, pneumatic equipment is not a modern invention. Over 2,000 years ago, Heron Alexandrinus discovered that compressed air increases power. Easily manufactured and transported, Heron’s equipment inventions form the basis for contemporary pneumatics.
Modern pneumatics
Today, pneumatic equipment includes everything from riveting and jackhammering to powering large equipment. And with increased complexity come certain risks, repairs, and maintenance requirements to ensure manufacturing employees can perform their jobs without injury or downtime.
Modern pneumatic systems still follow Heron’s basic design of sending air through a tube to create force. Pneumatics use compressed air as opposed to hydraulics, which use compressed fluid. The former is a relatively safe, cost-effective, and clean equipment-powering method.
Pneumatic maintenance and safety
Compressed air does involve some risk, but manufacturing professionals can lessen it with simple maintenance checks and immediate repairs.
Proper system design is the first safeguard against hazards. A simple design should allow ample room for the required pipeline network to supply power to the outlets needed to run the machinery. If more outlets are required after installation, consult a professional designer to properly install the new outlets and ensure the system will safely support the additional equipment.
Performing basic maintenance on a regular schedule can also help reduce system failure risks. Some items to check daily include compressor lubricant levels and belts. Regularly check for system leaks, especially around valves, hoses, and clamps. Anywhere the main pipe splits is prone to leakage. Periodically, examine system components and filters for debris and buildup, and replace filters per manufacturer recommendations.
Troubleshooting
Should your system require repair, always make safety your top priority when troubleshooting problems. The first few steps may seem obvious, but they are critical to safety: Relieve air pressure in the tank and shut the electricity off prior to performing any maintenance or troubleshooting.
With schematics in hand, visually inspect the system to see if you can easily identify the problem. If the problem is not apparent, power the system slowly to check its air pressure and whether parts fit properly or vibrate excessively. Once you shut the system down again, check to see if any air remains in the system as this residual pressure may trigger a malfunction.
Even though pneumatic systems date back thousands of years, modern advancements mean they sometimes require professional repairs. One of the most important safety aspects when dealing with any machinery repair is to avoid taking on tasks you can’t handle.
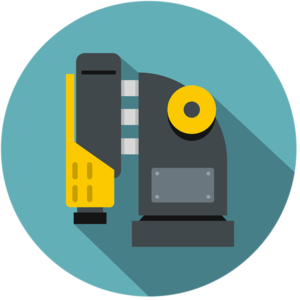