The Occupational Safety and Health Administration (OSHA) places a major importance on safety in the workplace, and pneumatic hand tools are no exception. In fact, in the OSHA “Hand and Power Tools” guide, the administration reminds those who work with such tools under OSHA regulations that it’s sometimes difficult to see the potential risks these tools pose as they’re so common in the daily lives of so many manufacturers. But, with the proper focus on safety, manufacturers can prevent incidents in their facilities that could cause harm to themselves and their co-workers.
Basic safety measures
For all who use power hand tools, it’s important to keep a few safety basics in mind. Whether they realize it or not, manufacturing professionals who employ these assets — even those who are well-trained in using them — are at risk of electrical accidents due to the nature of these tools and the work they do such as falling and flying dust, dirt, fragments, and other debris, and many work with dangerous materials. To prevent against these accidents and others, OSHA offers five basic safety measures to keep in mind:
Ensure your plant leadership provides the proper personal protective equipment (PPE), and be sure to use it correctly.
- Always use tools as their manufacturers direct.
- Inspect each tool prior to use, and never use a tool that’s damaged.
- Match the correct tool to its proper use, and never use a tool for work it’s not designed for.
- Maintain tools to keep them in proper working condition.
Pneumatic hand tools
According to the OSHA guide, “Pneumatic tools are powered by compressed air and include chippers, drills, hammers, and sanders.” And, in addition to basic hand tool safety, it’s important manufacturing leaders post signs warning employees about areas in which their co-workers use pneumatic hand tools. Shields or screens can also help protect those not working with pneumatic tools from accidents as well as protect them from the noise associated with their use.
And, of course, with air hoses connecting pressurized air to the tools, manufacturers should ensure the hoses they’re working with don’t present trip hazards for others on the plant floor. Another aspect to keep in check is to carefully monitor the connection between the air hose and pneumatic tool so they don’t disconnect, usually by using a fastener or lock. While regulations depend on the tool type, all pneumatic tool users are required to protect their eyes and faces, with hearing protection also required for noisy tools.
When manufacturing professionals keep these basic safety measures in mind and maintain and repair their pneumatic hand tools as necessary, they can prevent accidents and injuries associated with pneumatic hand tool use.
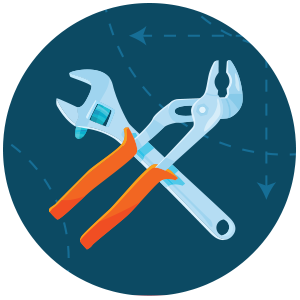