Hydraulic systems are common in many industries, including manufacturing, because they enable workers to perform a diverse range of operations via remote control. But they’re deceptively powerful machines, storing approximately 2,000 pounds per square inch of hot liquid under immense pressure. And safety training is often not required for people who work on or around hydraulic systems. In fact, “Over 80% of the people working on and around hydraulic systems have never received any training in hydraulics at all.”
Compounding these risks, myths abound about how to properly work with hydraulic systems. Misuse of hydraulic machines can result in severe injury, so it’s important to separate fact from fiction, practice important safety measures, and take precautions.
Hydraulic falsehoods
Do you recognize any of these common misperceptions?
If the unit is turned off, pressure is released from the system.
False. Hydraulic systems are designed to store liquids under high pressure in multiple areas, even if the systems are shut off or the machines break down. Therefore, it’s important to release pressure in all components and discharge the accumulator before performing maintenance, disconnecting lines, or adjusting components — even after the machine has been turned off or has malfunctioned.
Lowering a hydraulic system dissipates pressure in the system.
False. It’s not enough to make sure the unit is in the down position. You must manually relieve the pressure, including in the counterbalance, even after lowering the load.
Hydraulic machines don’t need maintenance.
False. Worn hoses, dirty components, and rusty rods can lead to failures, according to the “Hydraulic systems safety” article. Maintain hoses, lubricate rods, and clean pressure valves on your hydraulic systems to keep them operating within safe guidelines.
Three common — and avoidable — hydraulic injuries
Three kinds of injury are common when working with hydraulic systems. It’s important to be aware of these common injuries and the precautions you can take to prevent them.
- Burns — Intense pressure in hydraulic systems creates an extremely hot liquid, which can expel with force and cause severe burns. Always release pressure in units before working on them.
Bruises, cuts, and other injuries caused by flailing lines — Thrashing lines act like whips full of hot oil, inflicting injuries to those using hydraulics and anyone nearby. Always relieve hydraulic pressure and discharge accumulators before disconnecting lines.
- Injection of hydraulic fluid into skin — One of the most common injuries is the result of pinhole leaks in hydraulic lines. In fact, according to the Fluid Power Safety Institute, “over 99% of the people who service, repair, and troubleshoot hydraulic systems have been subjected to the exact dynamics that trigger a high-pressure injection injury.” Pinhole leaks aren’t easy to see. According to the “Hydraulic systems safety” article, many people only notice an oily spot on the line and instinctively run a finger along the hose to detect the leak. A high-pressure stream of liquid can propel through the pinhole at a high speed and inject itself into the skin with force, similar to a hypodermic needle. It may not be noticeable at first, but it can soon become swollen and painful — and can result in amputation. Never run a finger along the hose to detect a pinhole leak. Always use a piece of wood, cardboard, or plastic instead.
Knowing how these powerful hydraulic systems operate, implementing important safety measures, and taking precautions against common forms of injury are some ways you can maintain a safe hydraulic working environment for yourself and those around you.
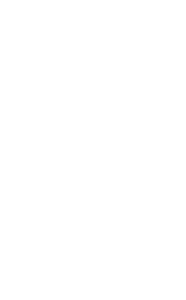