While its initial installation requires investment, robotic technology can offer great returns. In parts one and two of this series on automation and the manufacturing job market, we covered reasons behind the worker shortage and ways to mitigate the issues automation can cause. What else do those wanting to scale up production with robots need to know about automation as it relates to their workforces?
Robots on the rise
Manufacturers are increasingly turning to automation because, while labor costs continue to rise every year, the cost of robots has decreased substantially since 1990. In fact, the average labor cost-savings is around 16% in developed nations, but some manufacturers in Asia have seen savings as high as 25-33%.
One facet of automation difficult for many manufacturing leaders to accept is that some jobs will be lost. However, manufacturers can offer training programs for displaced workers to learn the skills they’ll need to enable increased earning opportunities when they re-enter the workforce. Another option many manufacturers are turning to when they need to increase their skilled workforces is strategic partnerships. They work with high school as well as technical and community college leaders to recruit, train, and hire fully trained and ready newcomers. Others opt to recruit then train through apprenticeships post-hire. As automation helps increase productivity while reducing costs, the manufacturing industry may indeed become a larger part of the American landscape.
Suggestions for manufacturers looking to automate
Are you looking to automate your manufacturing plant? It’s imperative you know where to start when it comes to your workforce.
- Determine which activities to automate based on your company’s main business objectives. These may include simple, low-cost automation updates as well as expensive, fully-automated, high-tech solutions. Choose those that allow your team members to reach primary company goals better, faster, easier, and more effectively.
- Calculate the return on investment you expect from automation compared to your human workforce. It’s easy to overspend on automation, so make a detailed plan. With human capital in mind, figure out exactly what problems your automation systems will address and how they will affect your bottom line over the next several years.
- Consider the flexibility inherent in your potential automation solution. If you opt for a rigid system that only works for one specific product, it will likely be time-consuming and expensive to change or update products, thus requiring human intervention. Consider how flexible and adaptable your chosen automation solutions should be when conditions change. Would it be more beneficial to retain employees in certain areas to address potential issues?
- Consider how your automation solutions should integrate with the rest of your production facility and how it could impact workers. How will the new system network with your other equipment and data systems? Will your automation plans include cobots? How much training will your team require?
Automation can offer manufacturers the ability to increase production — even amid a worker shortage — without sacrificing quality. It also allows them to be more competitive, cut labor costs, enhance worker safety, and adapt to changes more readily.
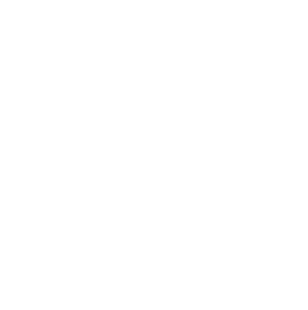