A good industrial maintenance program tracks a slew of metrics. One of the most important is mean time between failures (MTBF). A simple equation makes it easy to measure just how much uptime a machine is capable of between failures. It’s a useful figure for understanding the lifespan of certain parts or the effect of certain catalysts on a machine’s operability. And most importantly, it provides uptime information that’s vital in creating proactive and preventive maintenance plans.
Understanding the metric
The equation for MTBF is simple: total production time divided by the number of failures. For example, if a machine runs for 500 total hours and has 10 total failures, its MTBF score is 50. Generally, the higher the MTBF score, the more reliable a machine is.
Tracking MTBF is important because it’s a direct measure of total uptime, as well as the average time between failures (as the name implies). It’s one of the core key performance indicators (KPIs) used in lean processes for determining reliability.
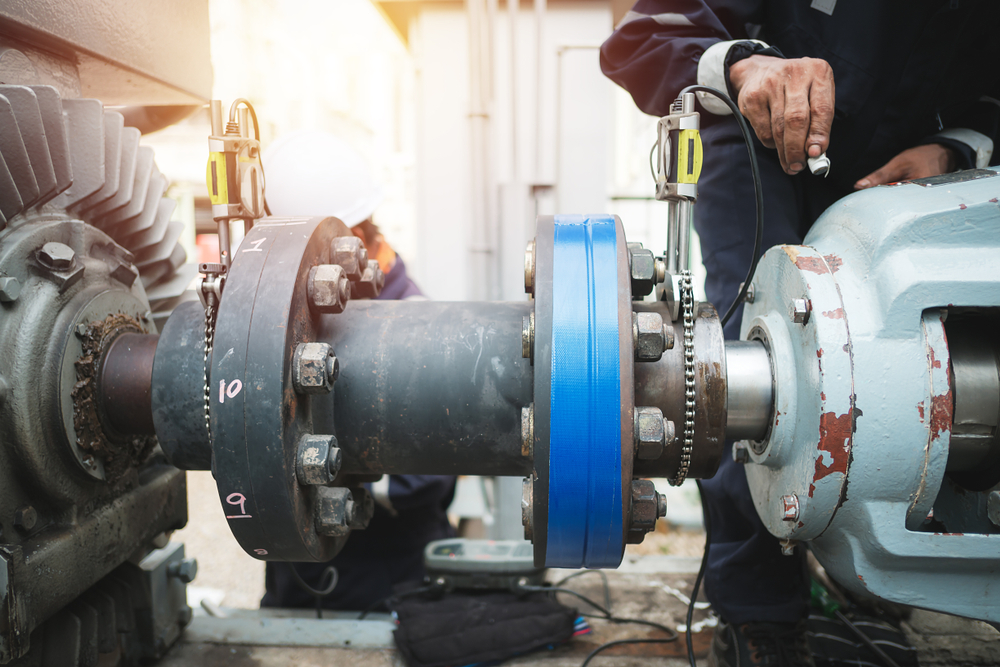
It’s not a foolproof metric
Despite its usefulness, MTBF is often relied upon for much more than it’s meant for. In fact, several myths have arisen about how to use MTBF or what it can tell us. Let’s take a look at three of them and provide a little context for what the truth actually is.
Myth 1: MTBF is a month-over-month variable. This myth is partially true, but mostly just an incomplete truth. Although looking at MTBF each month does yield insight, the better approach is to look at cumulative MTBF over several months. Don’t assume a constant failure rate! To get a clearer picture of MTBF, run the equation monthly, then quarterly. You might be surprised to see a different picture of reliability. See a great example of this here.
Myth 2: MTBF by itself is enough to qualify reliability. While MTBF is an indicator of machine reliability, it’s hardly the only factor involved in making that determination. If you’re only using MTBF, you’re ignoring other variables such as frequency of maintenance or catalysts for failure. Using MBTF as the only benchmark for reliability means assuming uniform runtime, and that’s just not accurate. Combining it with mean time to repair (MTTR) and mean time to failure (MTTF), for example, give it context and meaning within a broader scope of reliability.
Myth 3: MTBF is useful as a single data point. Wrong! MTBF needs to be viewed as a trend. Similar to the first myth above, trying to use one measure of MTBF isn’t going to provide insight. For example, if you have one machine that runs for 100 hours and fails two times, your MTBF is 50. But that’s just one month. The next month it may run for 100 hours and fail six times, then 12 times, then 16 times. Looking at each instance of MTBF alone only yields insight for that month; looking at each instance linearly paints a picture of increasing failures.
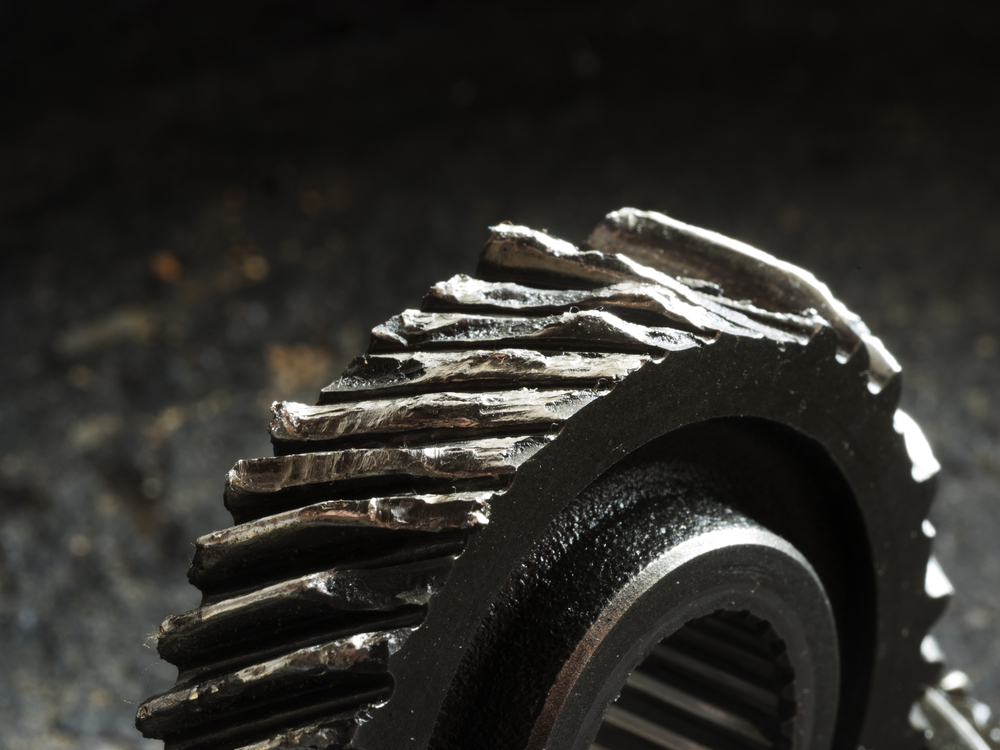
It’s important to recognize and understand these myths. Abuse of the MTBF score is prevalent in many industries today because it’s a convenient number to work from. The problem is that it’s often used as a standalone metric, instead of in conjunction with others (MTTR, MTTF). If you’re planning on gleaning information from MTBF, use it for what it is: part of a more robust reliability measurement.