Like any tasty recipe, manufacturing business leaders need a few main ingredients to start things off and maintain strong consistency as they add more products to their offerings. For manufacturers, this means establishing plant efficiency and productivity. If you remove one ingredient from either the recipe or the manufacturing plant the results can be problematic, bland, flat — or not work at all.
Efficiency begets increased productivity. Without efficiency, productivity decreases, employees and management are unsatisfied, and the company could be at risk. Living in an economy in which productivity dropped 0.6% during the first quarter of 2017, crafting efficient plant standards and maintaining them can put you ahead of competitors. To get to this level you need to look at three items: equipment, processes, and personnel.
Equipment and Processes
These two items together represent the Overall Equipment Effectiveness (OEE) of your plant. OEE is used to uncover inefficient production processes by examining equipment and personnel availability, performance, and finished work quality. The compiled OEE provides pertinent information on what plant leaders can improve to reduce operating costs. For instance, they may need to change out older machines for energy-efficient equipment with increased automation and output. In some cases, manufacturing decision-makers may replace two machines with a single newer model that does both tasks more efficiently.
Personnel
Examining equipment and the processes required to run it isn’t the only solution. Personnel at all levels also need to examine where they can increase efficiency and productivity.
In many situations, employees crave additional training. With automation taking over certain positions on the line and more machines joining part of the Internet of Things (IoT), older employees sometimes feel they can’t compete with new talent, and this drives their productivity down. Ongoing equipment training and cross-training can help boost all employees’ confidence. And when they’re cross-trained, decreases in efficiency and productivity rarely occur as personnel can take charge of equipment when those regularly assigned to certain positions aren’t available.
Recipes work best when chefs smoothly combine all ingredients together. The same goes for a manufacturing plant: When equipment, processes, and personnel are correctly put together the result is a smooth-running manufacturing plant that exceeds the competitors’ efficiency and productivity.
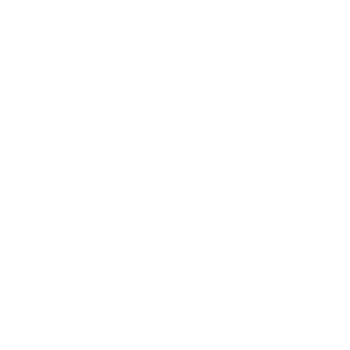
The most crital engineering is the one that designs the construction process. The only thing that is constant, is change. If you have a desighn that cannot be changed quickly and efficiently you are at a huge disadvantage.if you must produce quickly,do so but, do so in increments that can be changed even quicker.