Cross-training has been closely connected to athletics for years. Consider quarterbacks: In addition to running to keep their legs strong and limber as well as their cardio strong, quarterbacks cross-train using weights and yoga to increase their strength, stamina, and flexibility. You don’t have to look far to find examples of hockey players, basketball players, and running backs doing yoga.
Yet a cross-training strategy isn’t only for athletes. Implementing it can also improve your production line operation while allowing your team to create a culture of success. And when you become part of the process, you don’t simply increase efficiency. You create a learning organization. The main concepts behind this are analyzing and adapting to address inefficiencies and achieve greater success. If this sounds intriguing, here are some ways to institute a cross-training strategy in your organization:
Prioritize
Review all production line operations and start asking questions. For example, where are workloads largest? What part of the production line is the most mission critical? Where do you see most bottlenecks? Do you have more fail-safes at your most-critical line portions instead of least important? You may think you know the answers, but a concentrated review can reveal incongruences that have developed over time.
Determine relationships
During your review, you may see production line areas in which cross-training would work because of operation similarities. These are your obvious trainings, which you should take care of as soon as possible. Once implemented, you may see considerable impacts and bottleneck reductions at those parts of the line. When you complete these obvious cross-trainings, review the line again to determine who should participate next.
Set them up for success
Showing everyone how to work a production line component one time is not efficient cross-training. Why? Basically, not all employees have can absorb all the information immediately. Like cross-training in athletics, it takes practice and patience to get employees up to speed. Therefore, arrange for practice times in different areas for your employees to get used to other line parts. If this doesn’t feel comfortable, have one set of employees shadow another set of line workers to see how they do things.
Ask, don’t tell
Forcing employees to cross-train in one production line area when they want to work in another is counterproductive. However, listening to employee requests to train in certain areas can provide a positive strategy. Allow them to offer input into their own paths to set up productive and happy work environments.
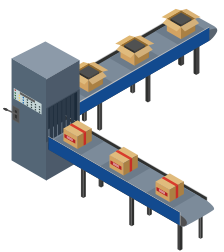
If you have industrial electronic, servo motor, AC or DC motor, hydraulic, or pneumatic needs, you can contact us by phone at 877.249.1701 or here.