Since the Industrial Revolution in the 1800s, industry has been continuously evolving. Over time, we’ve gone from assembling products by hand to 3-D printing. This progress can be broken down into four main eras of production history:
- 1800s: Water and steam power were utilized to create mechanical production facilities. This was the first step in the transition from hand production to machines.
- 1900s: The advent of electricity encouraged the assembly line, which enabled mass production.
-
2000s: With the emergence of computers and early automation, robotics and information technologies began to replace laborers on the assembly line.
- Today (Industry 4.0): The next step in automation and machine learning, as well as the emergence of “the smart factory.” Within this factory, the goal is for decentralized decision-making to occur, which the Forbes article notes as, “the ability of cyber-physical systems to make simple decisions on their own and become as autonomous as possible.”
In the early 2000s, advances in technology allowed manufacturers to automate their factory production lines. Today, the Industry 4.0 model breaks through the confines of the factory walls by helping to streamline the entire value chain. The big step is moving from a world of automation to a cloud-based system.
Industry 4.0 involves three key features:
- The Internet of Things (IoT) and cyber-physical systems: IoT, the computing technology embedded in devices that allows communication with other devices and people through the internet, is used to collect data not only from within the manufacturing control system, but also from the users.
- Advancements in big data and powerful analytics: Technological advancements have allowed systems to rapidly search through the huge data sets to produce solutions that can be implemented almost immediately. In fact, 72% of manufacturing companies predict the use of data analytics and big data will improve customer relationships.
- Secure communications infrastructure: Cybersecurity is becoming more advanced. With so many devices becoming interconnected, the supply chain can be especially vulnerable, resulting in a continuous push for advanced protection.
Industry 4.0 also provides the framework for manufacturers to use additive manufacturing (or 3D- printing) technology at scale to produce end-products and customized machine parts within the supply chain itself.
This new industrial transformation is in its early stages. Innovators are constantly developing and redeveloping new technologies. There is no quick way to implement Industry 4.0 methods. The best way to approach the addition of Industry 4.0 to your production line is through small test projects. This will help you better understand the advantages and disadvantages of adopting these new technologies at scale.
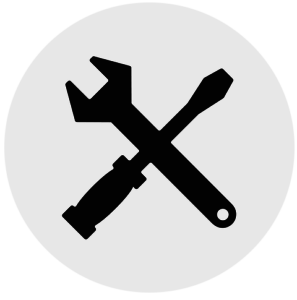