Today’s manufacturing sector is more competitive than ever. Line shutdowns cost money, either in lost productivity or — worse — lost sales.
Maintenance schedules help manufacturers manage production line updates and repairs. Developing a strategy can help you reduce downtime while keeping losses to a minimum.
Base strategy on reality
Before you can establish your plan, you need to know how your systems work, where they show potentials to fail, and potential failure costs.
Inspection
Each machine fails differently, and downtime to repair or replace each machine’s parts differs. Study each machine’s last repair or service update and gather your data. Consider the following as you look at each failure and repair:
- Reason for or nature of the failure
- Production team response
- Cost to fix the problem(s)
- Time spent to get back online
If a failure was unexpected, identify cost to the company while the machine was offline.
You’ll need to comprehensively evaluate each machine’s performance within the system. Tracking repairs — even minor ones — gives you data you can use to develop standard maintenance calendars.
Preparation
After your assessment, inventory your spare parts and accessories. Be sure to have incidentals and supplies in stock before you need them so you don’t waste time in acquisition.
Identify a strategy
A maintenance strategy can help you reduce the need for reactive repairs as well as optimize asset life and productivity. A proactive strategy should include the following:
Preventive maintenance
Virtually all machine parts will wear down over time and need replacement. Keeping them running well for the longest possible period requires both minor and major attention.
How do you do this?
- Minor maintenance ensures that each machine will perform reliably in response to demand. A reliability-centered maintenance strategy calls for regular routine maintenance tasks — lubrication, cleaning, filter changes — to ensure optimal operation.
- Major maintenance addresses failure potential. Components erode at different paces, and replacing them may not require major intervention. If enough parts are approaching the end of their anticipated life spans, however, it may be time to replace the machine altogether.
Predictive maintenance
Once you understand your system’s physical conditions, you can launch a predictive maintenance plan. Based on data you garner from your assessment, you can use technology to predict machine and part life spans so you can schedule repairs and maintenance before they fail.
A regular maintenance schedule can help you anticipate both major and minor maintenance so you can minimize downtime and keep your shop productive and safe.
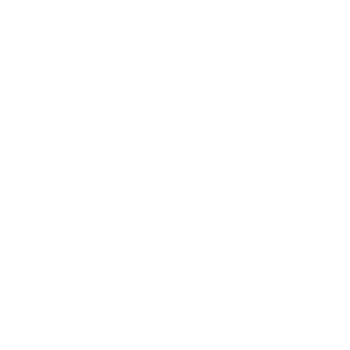